EOT Crane Anti-Sway Control
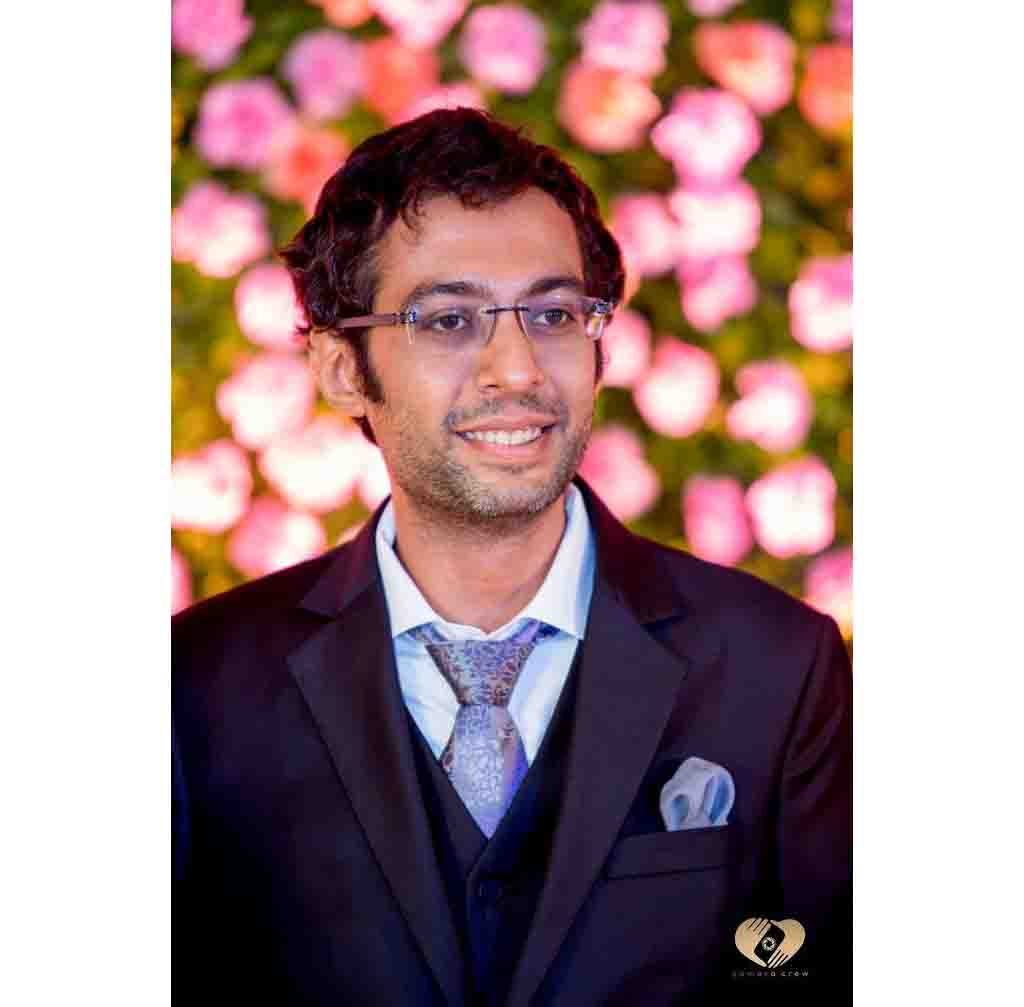
In todays Blog we will discover what is
EOT Crane Anti-Sway Control
Why they are used? What are the benefits of Anti-Sway Control?
So if you want to make sure that your knowledge of the EOT Crane Anti-Sway Control
is up to speed, you should get a lot of value from today’s content.
- Working of the Anti-Sway Control
- Types of Anti-Sway System used in EOT Cranes
- Benefits
- Conclusion
Introduction
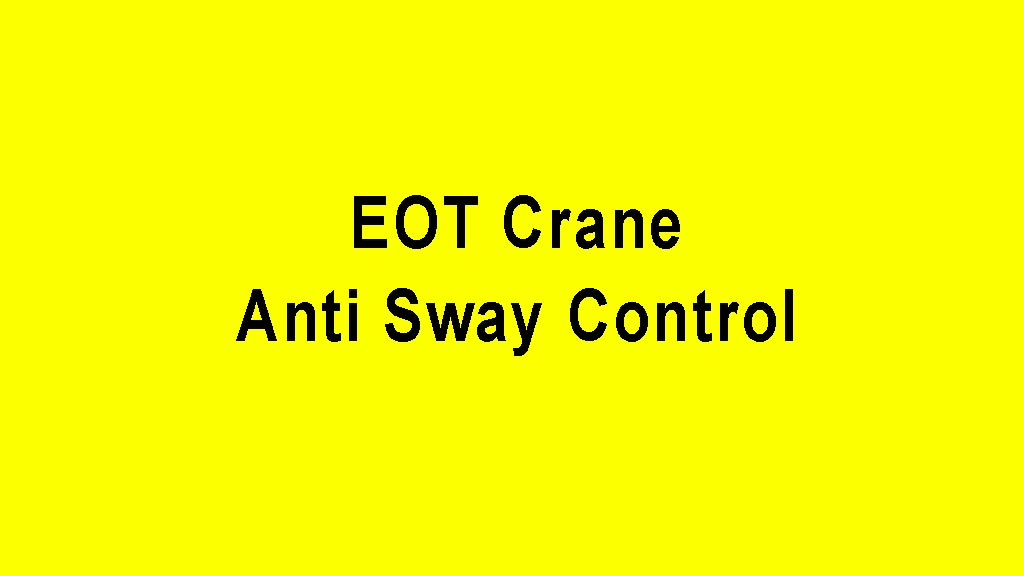
While operating the crane, the crane operator needs to make sure that there is very less crane
swing while moving the load. The swinging of the crane takes place when the crane is moving in
one direction very fast and due to this, the momentum forces it to moves back and forth. This
can create a very dangerous situation on a worksite.
To avoid this kind of situation, Anti-Sway Control is used to monitor and control the crane
movement. Anti-Sway control controls the speed of the motor through PLC.
Working of the Anti-Sway Control
When the operator sends the command to the crane, the anti-sway
control translates the operator command into timed acceleration patterns. Then these timed acceleration
patterns are transmitted to the EOT crane’s PLC in the real-time. This pattern varies slightly from the
operator’s stick control or a simple speed ramp. There is a small difference in these pattern and
operator’s command so that it can avoid the swaying from the motion of the trolley.
If in any situation, the operator moves the control at a full speed, then the anti-sway control will
accelerate initially according to the operator’s demand, and will also induce the initial load sway.
When half the reference velocity has been reached, the anti-sway maintains the constant velocity for
a short time. Then this time the trolley is accelerated again by the operator’s command velocity.
This another acceleration eliminates the sway which is induced by the first acceleration.
Now the
trolley is travelling at the operator command’s velocity, along with the load hanging below the trolley.
When the operator releases the stick for zero velocity, then the same process is repeated in reverse,
so that we can stop the movement without any sway. If the operator wants movement for a short time,
the anti-sway control will stop the motion and then perform the second movement to catch the sway.
All this operation requires precise and accurate timing, that is dependent on the natural frequency
of the pendulum motion. The anti-sway carefully manages the changes in hoist cable length, changes
in the operator’s command, etc. in the real-time.
Rather than using the real-time sway measurement and control feedback, the main features of the
anti-sway control use the precise timing of acceleration to control the sway.
However, when we need to eliminate the sway that has to occur because of wind or non-vertical lift
factor, the anti-sway control will measure and correct the actual sway in the real-time, usually at
the end of a move, within user-selected tolerances.
Types of Anti-Sway System used in EOT Cranes
-
Closed Loop System
The closed loop system measures the parameter of the movement of the load and decreases the swing of the moving load. It also eliminates the external influences such as wind load, as there is a feedback circuit present in it. The anti-sway control is included in the main PLC control of the crane. -
Open Loop System
The open loop system prevents and decreases the swaying movement of the load. However, it doesn’t protect from the external influences such as wind load, as there is no feedback from the actual load position.
Benefits
- It modifies the crane operator command to the crane motion drives so that the accelerating or deaccelerating while moving the load will not produce any swing.
- It allows the operator to use the full speed commands for all the movement, which will result in faster transit times.
- During the load movement, the control of the sway is effective, it doesn’t matter what the hanging length of the load is. Hence, the hoist is not required to full hoist height to minimize the sway. This allows the crane and trolley movement to start more quickly, which will again save the transit time.
- When in automatic control, it accelerates to maximum speed using the maximum acceleration at all times. To travel the crane and trolley at maximum speed at each direction are automatically calculated to produce a minimum time transit.
- If there is any obstacle in the path, the automatic control calculates the shortest path between the crane and destination.
- It provides safety for the crane’s load as well as the workers.
Conclusion
The implementation of the closed-loop anti-sway control system will prevent the load swing from a manual error such as the wrong alignment while lifting the load, and external influences such as wind load. It offers safety in the working environment.Please Call on 9137620579 for more Details.
Anand Systems Engineering is an Indian manufacturer of Radio Remote Control systems for Cranes and Hoists with a Goal of modernizing Indian Engineering.
Follow us on YouTube.