Electro Hydraulic Thrustor Brakes Manufacturer in Mumbai, India
Thruster Brake is used to halt the movement of a moving EOT crane machinery by applying a braking force to the shaft connected to an electric motor.
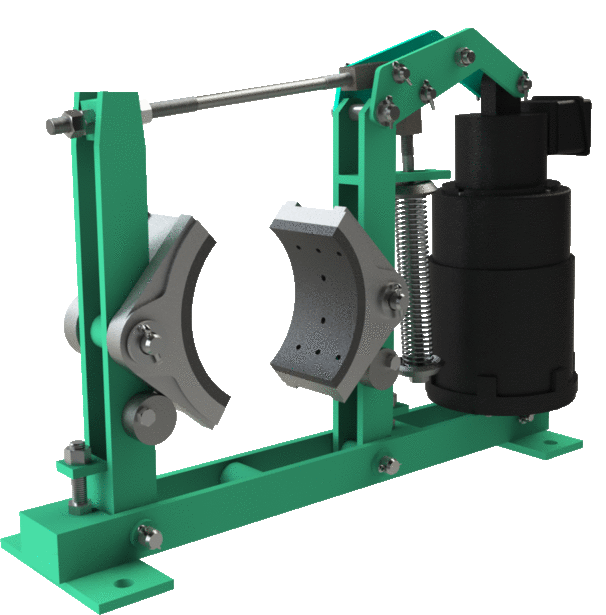
Latest Dispatch
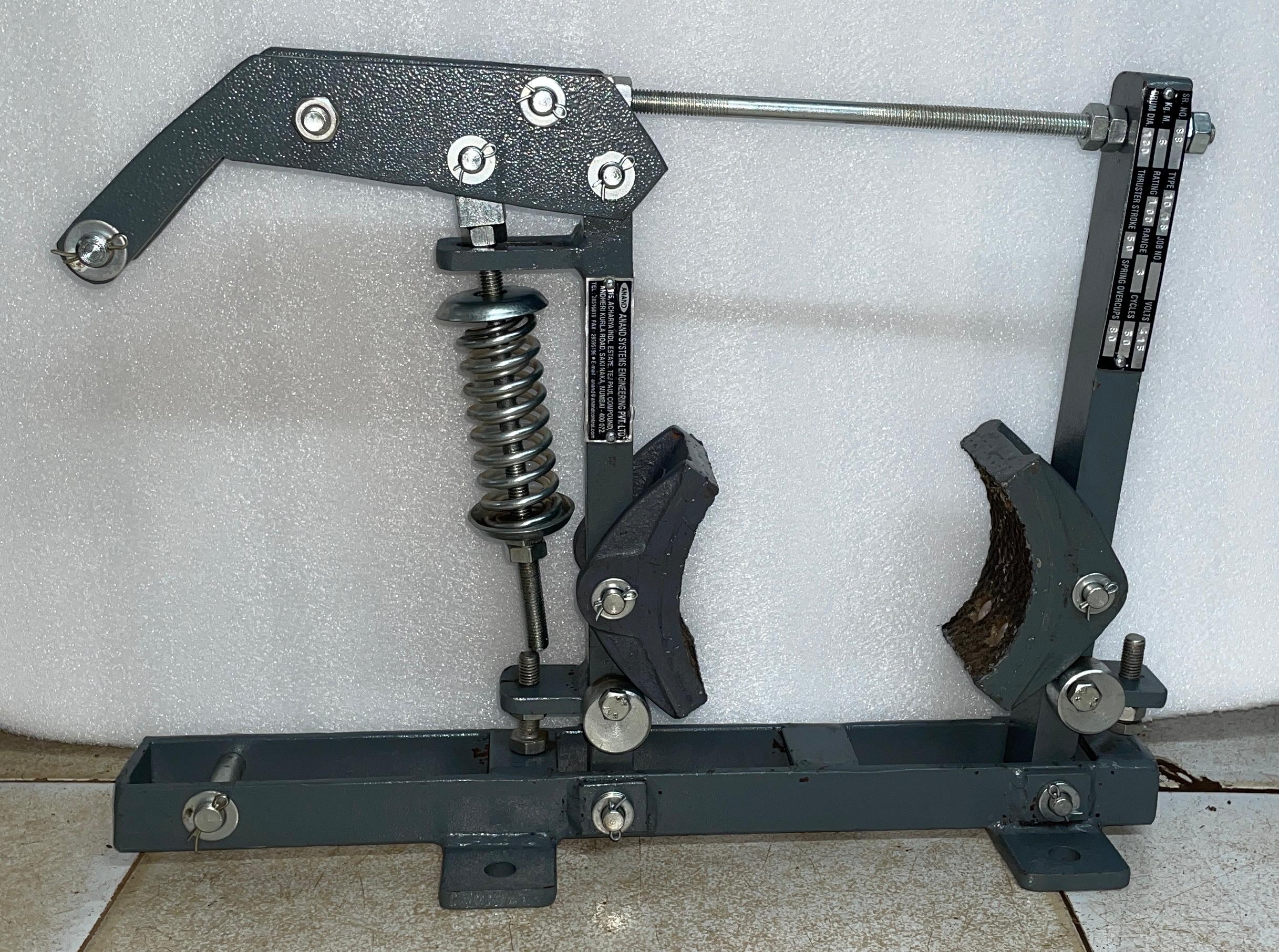
Fail-Safe Drum Brake Shipped
Today, we dispatched the Fail-Safe Drum Brake Shipped. Engineered for reliability, this brake assembly automatically engages via spring force to prevent load slippage during a power failure. It is designed to be operated by an electro-hydraulic thruster, ensuring controlled and safe braking for our client's crane systems.
Posted on June 30, 2025
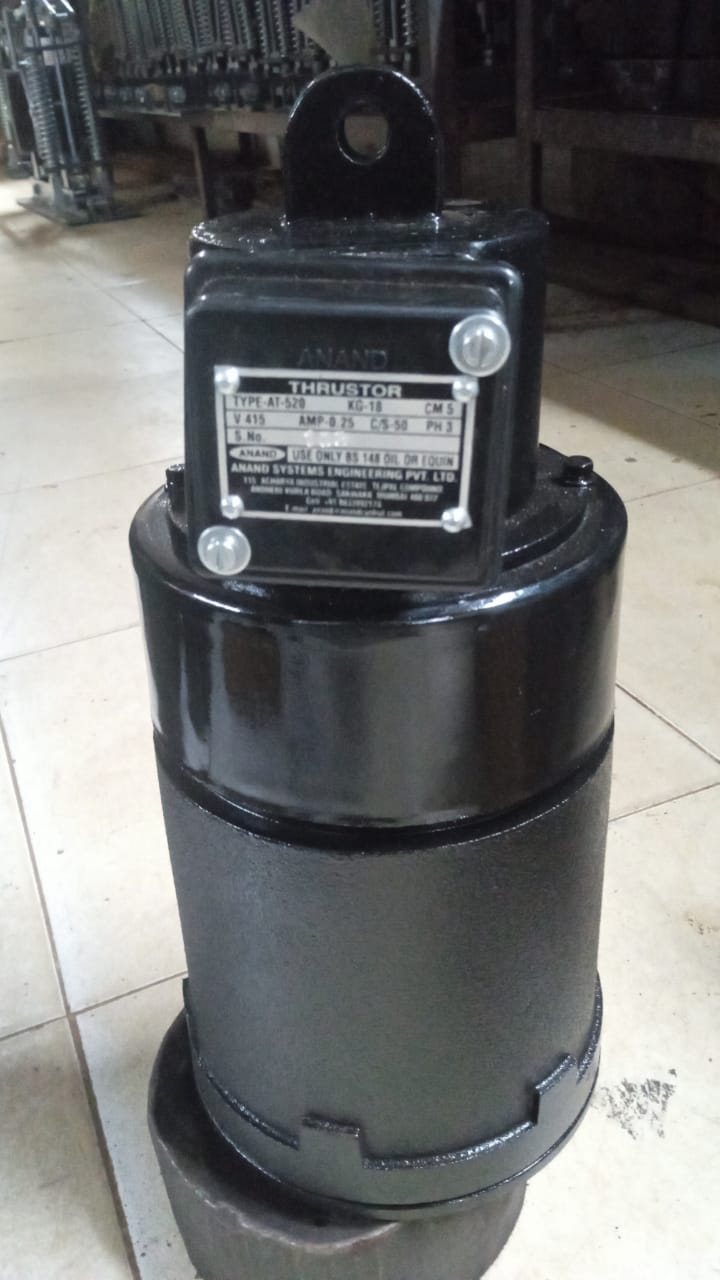
Thruster 18kg Dispatch
Today, we dispatched the Thruster 18kg.Our thruster and thruster brake are being used by a company that designs and services industrial cranes, helping ensure safe and reliable braking in their lifting systems.
Posted on June 30, 2025
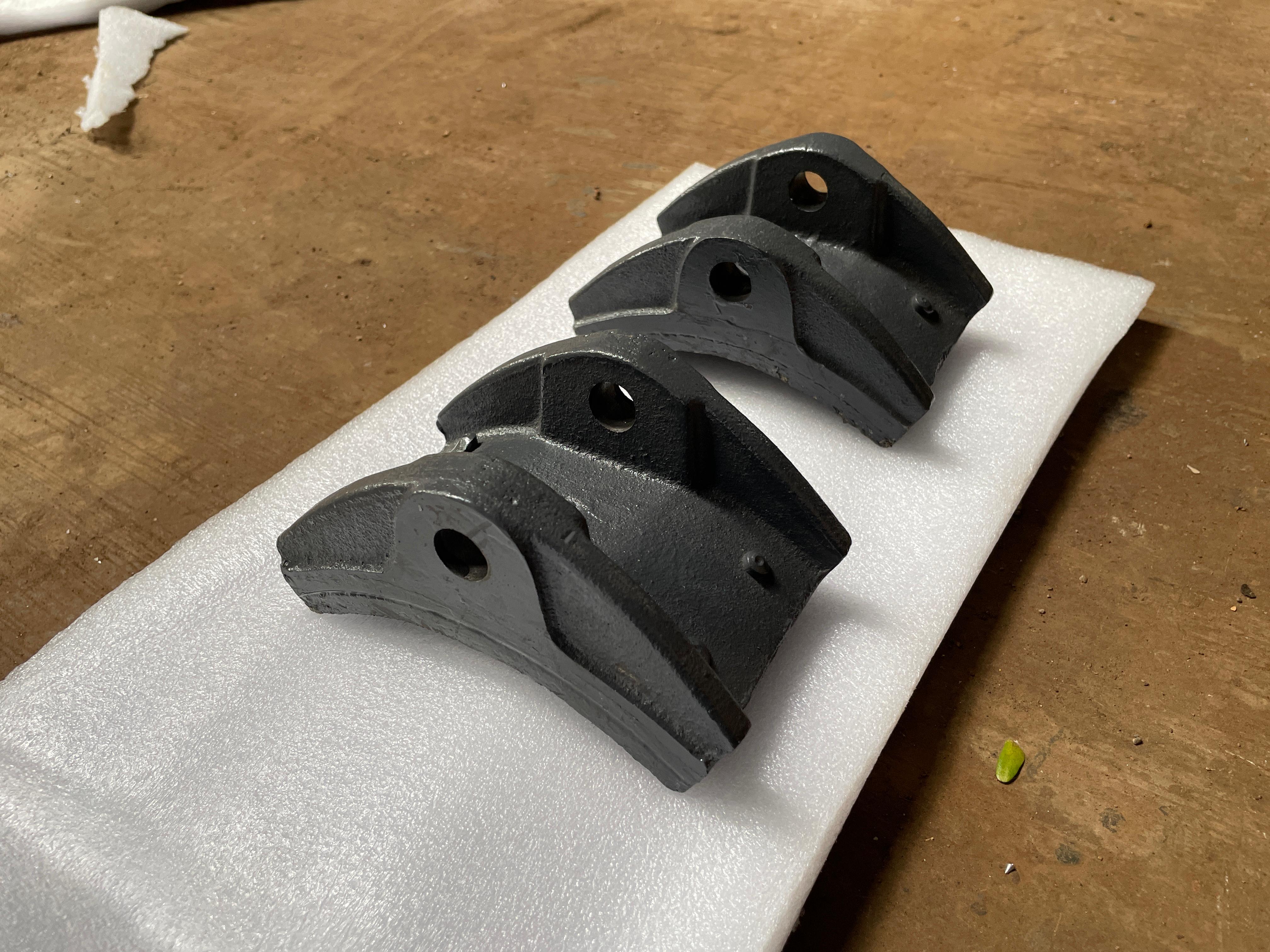
High-Quality Thruster Brake Shoes Dispatched
We are proud to announce the dispatch of our high-performance Thruster Brake Shoes. These are crucial spare parts for maintaining the safety and efficiency of industrial braking systems.
Each shoe is fitted with premium, non-asbestos friction lining to ensure maximum braking force, minimal wear, and a long service life. They are essential for the reliable operation of thruster brakes on EOT cranes and other heavy machinery.
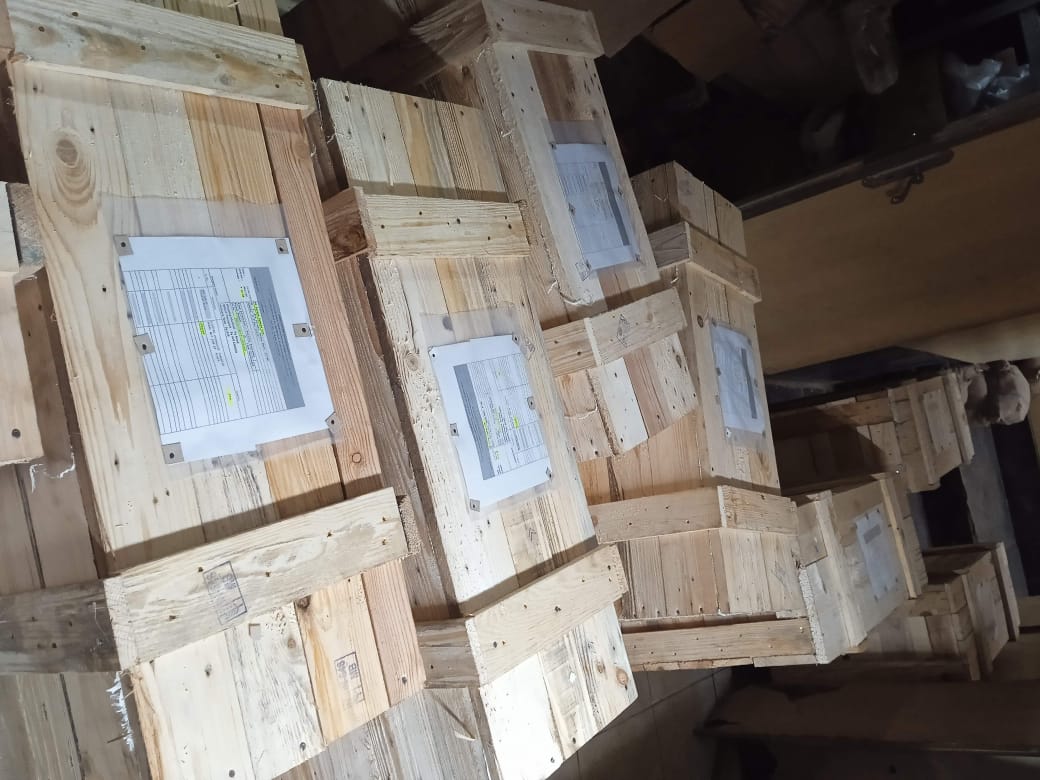
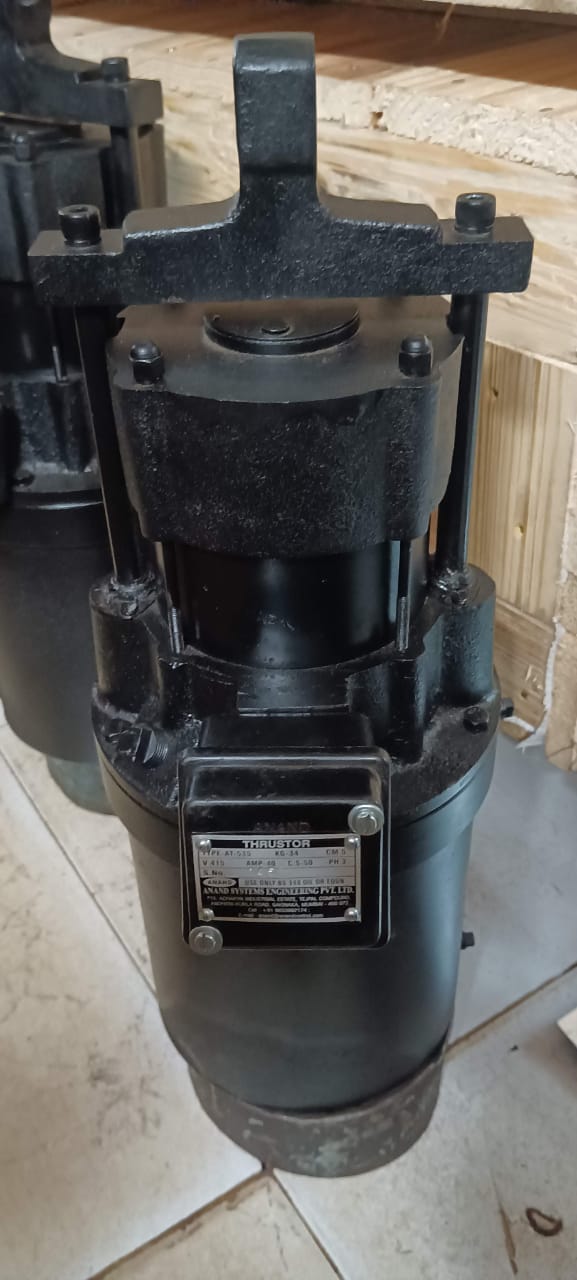
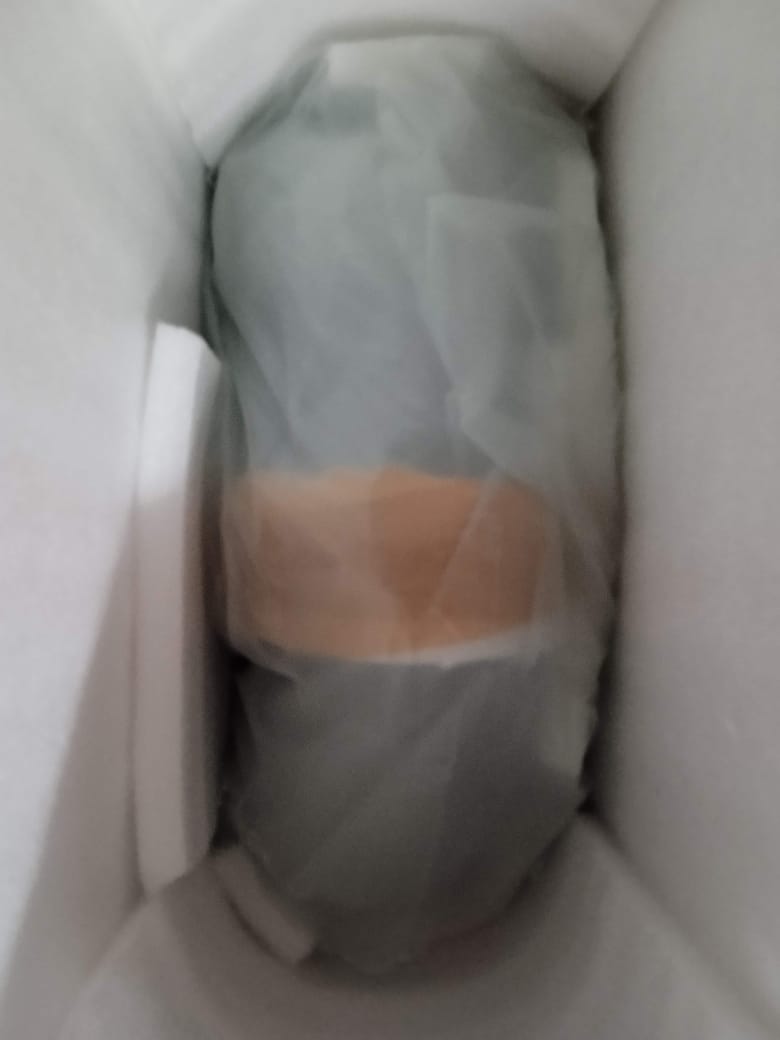
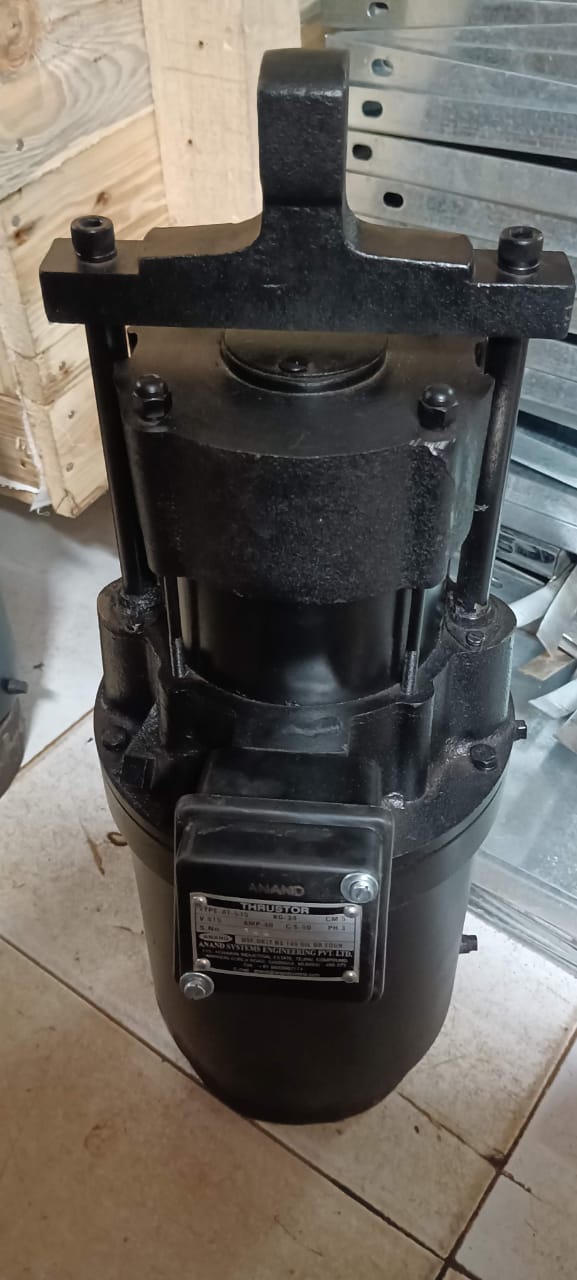
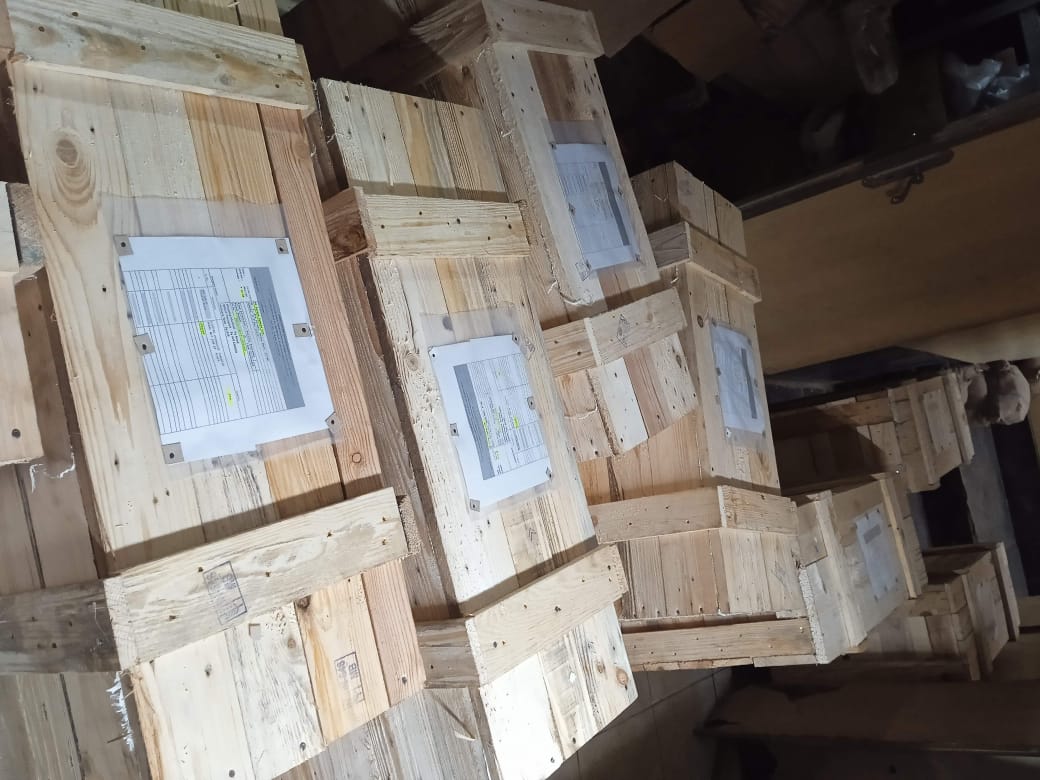
Thruster Dispatch
We are pleased to announce the successful dispatch of our premium-grade Thruster.
This consignment has been shipped internationally to Zambia, where it will support heavy-duty crane operations across industrial sites. Engineered for reliable braking performance under extreme load conditions, our products continue to contribute to global infrastructure and safety systems.
Posted on June 01, 2025
Watch our video for understanding Thruster Brakes for EOT cranes.
Premier Manufacturer of Electro-Hydraulic Thruster Brakes
Anand system engineering is a leading manufacturer of high-quality electro-hydraulic thruster brakes based in India. Products are designed for various industrial applications, ensuring reliability and superior performance. The team at Anand Control utilizes advanced technology and expertise to produce brakes tailored to meet customer requirements, providing custom solutions that adhere to the highest standards. Contact us for more information and elevate your industry performance with innovative braking systems.
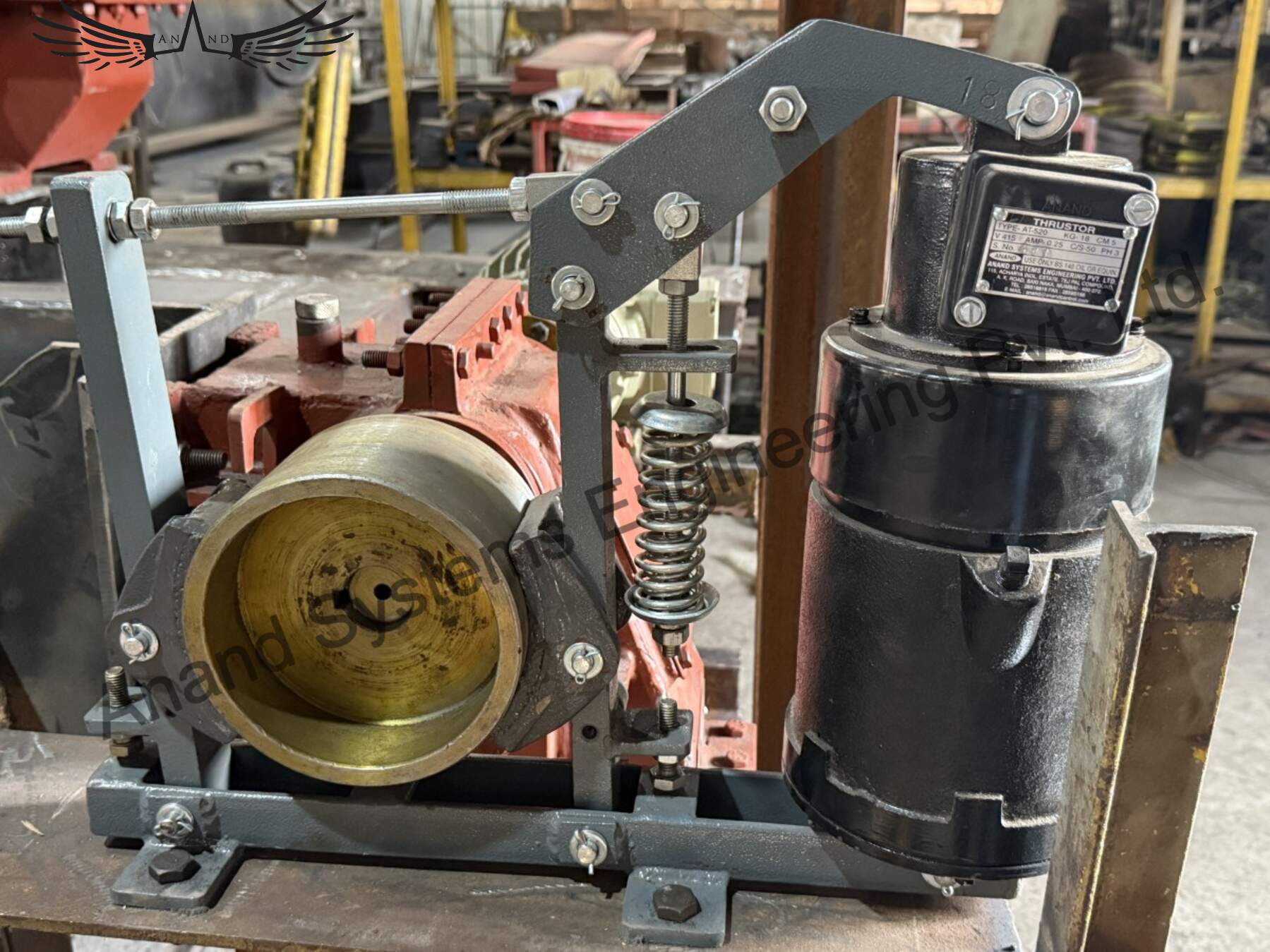
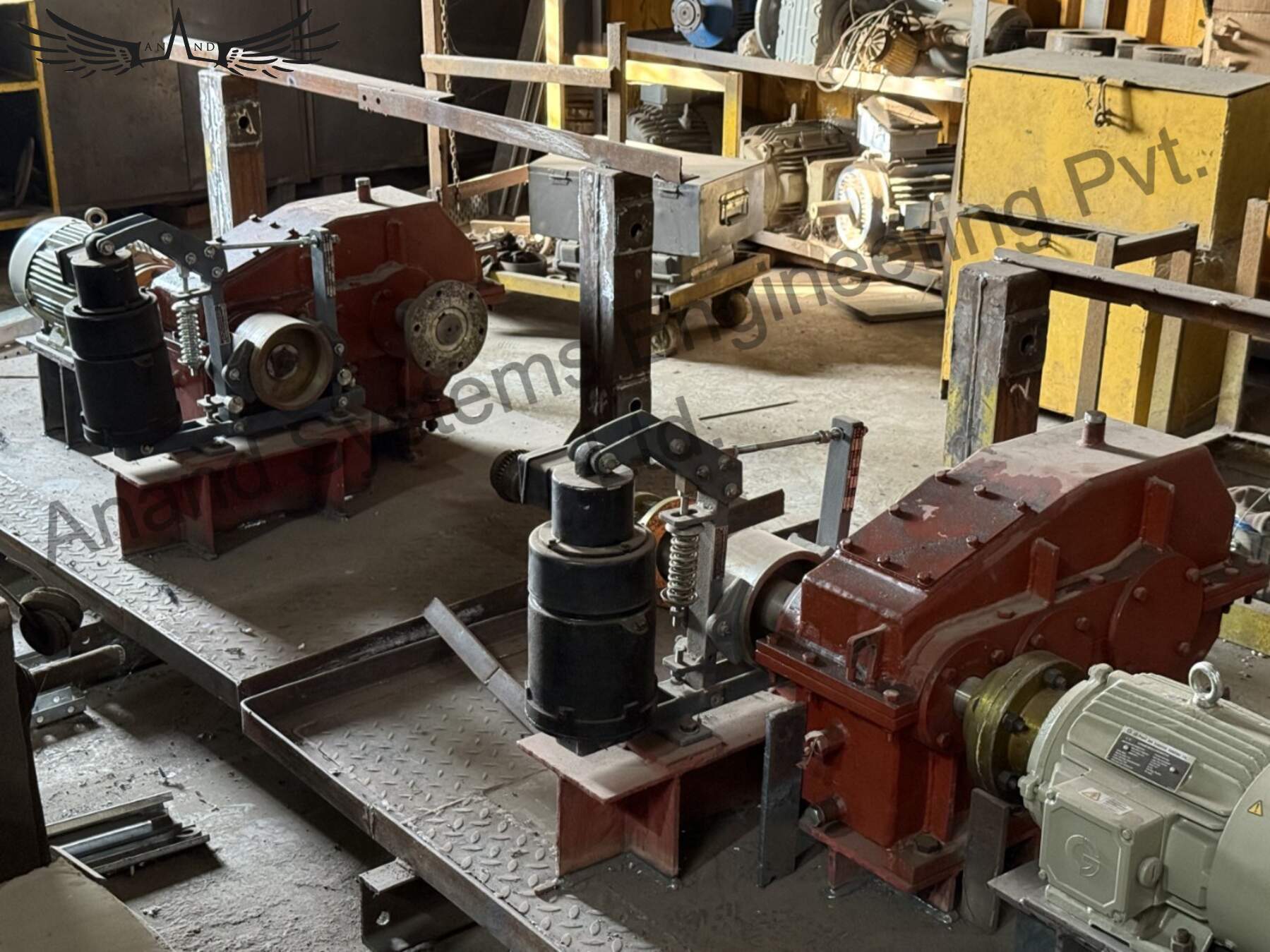
self-centering of brake levers
Automatic wear compensator
Stainless steel pins and spindles
Thruster Brakes for any EOT Crane
Enchanced Thruster Design along with robust steel frame & cast iron brake shoes
Select from 18-295 Kgs of Thruster:
The shaft of a three-phase electric motor is connected to an impeller inside a hydraulic cylinder filled with transformer oil. To prevent leakage of the transformer oil at the point where the motor shaft enters the hydraulic cylinder, oil seals are utilized. When electric power is supplied to the motor, the impeller rotates at the motor’s designated RPM, generating hydraulic pressure against the internal walls of the cylinder. This pressure causes the tie rods to thrust upwards, counteracting the external spring and activating the brake arms of the Electro Hydraulic Thruster to release the shaft.
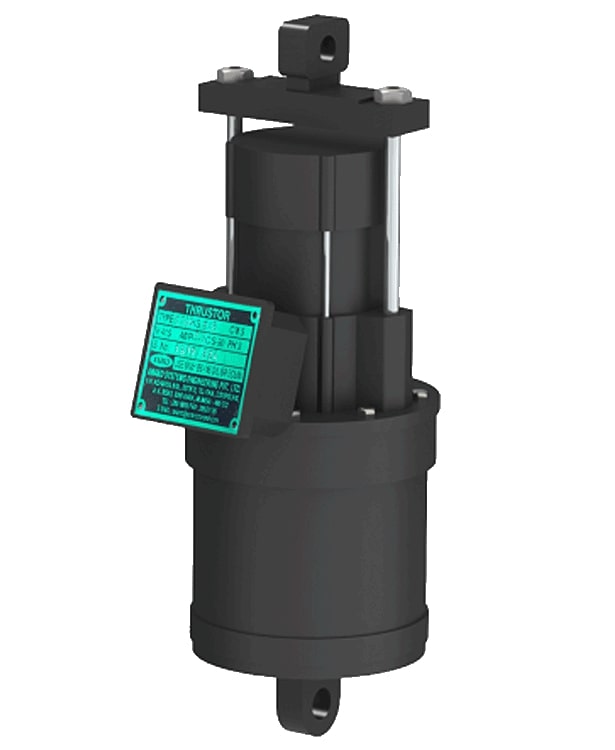
Steel Compression Spring
This steel spring is pre compressed during the installation of the thruster brake to constantly apply a force on the motor shaft through the brake shoe pads.The carefully chosen material ,pitch,diameter & number of active coils give the constant braking force required for a particular motor on the crane or elevator. When 3 phase electric power is applied to the thruster , crank lever moves upwards and releases the brake shoes which frees the motor drum. When electric power is removed from the thruster,crank lever comes down due to loss of thrust & with the force of the loaded spring and brake shoe pads now apply pressure to the rotating shaft.
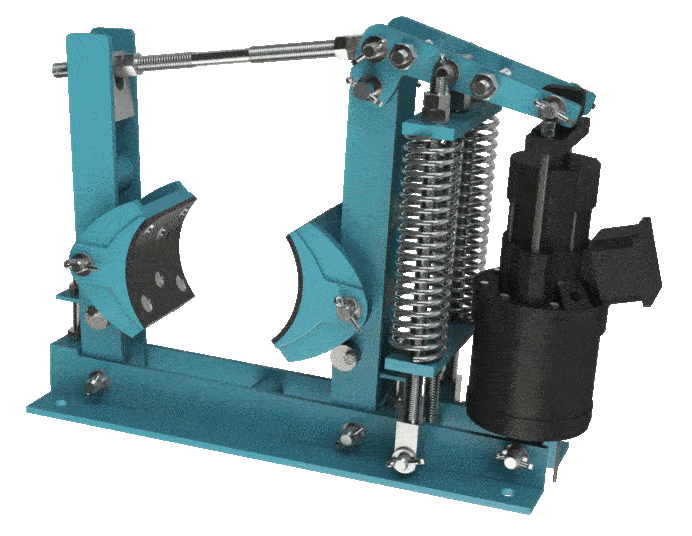
Heavy Duty Brake Shoes
An asbestos brake pads are used on the steel brake shoes to absorb the heat generated due to the friction of the shaft with the linings.The asbestos brake linings are riveted to the brake shoes and get worn off over time.
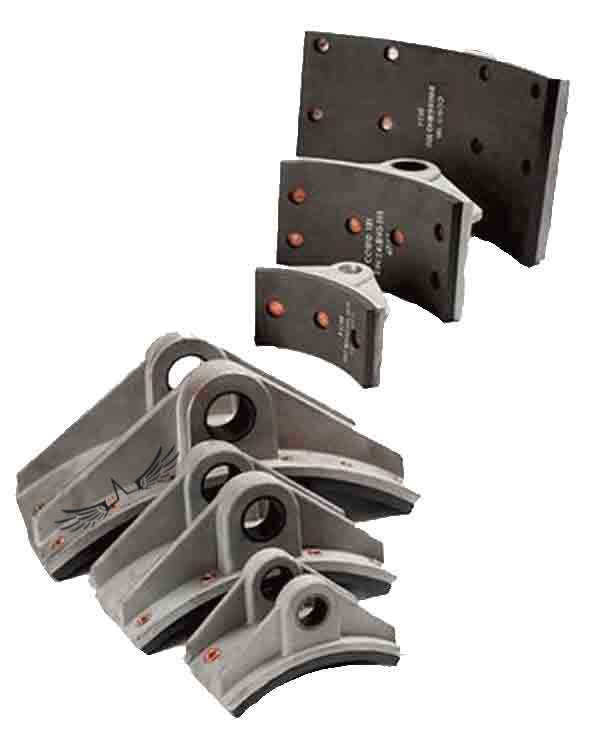
Product List of Thruster
Sr. no. | Product Name | Description | Part Number | Images |
---|---|---|---|---|
1 | 18 Kg Thruster | ELECTRO HYDRAULIC THRUSTER/MILL DUTY THRUSTER 18 Kg Thruster,HSN Code:84312010 | AT-520 | ![]() |
2 | 34 Kg Thruster | ELECTRO HYDRAULIC THRUSTER/MILL DUTY THRUSTER 34 Kg Thruster,HSN Code:84312010 | AT-535 | ![]() |
3 | 46 Kg Thruster | ELECTRO HYDRAULIC THRUSTER/MILL DUTY THRUSTER 46 Kg Thruster,HSN Code:84312010 | AT-546 | ![]() |
4 | 68 Kg Thruster | ELECTRO HYDRAULIC THRUSTER/MILL DUTY THRUSTER 68 Kg Thruster,HSN Code:84312010 | AT-870 | ![]() |
5 | 114 Kg Thruster | ELECTRO HYDRAULIC THRUSTER/MILL DUTY THRUSTER 114 Kg Thruster,HSN Code:84312010 | AT-8100 | ![]() |
6 | 226 Kg Thruster | ELECTRO HYDRAULIC THRUSTER/MILL DUTY THRUSTER 226 Kg Thruster,HSN Code:84312010 | AT-13200 | ![]() |
7 | 296 Kg Thruster | ELECTRO HYDRAULIC THRUSTER/MILL DUTY THRUSTER 296 Kg Thruster,HSN Code:84312010 | AT-13300 | ![]() |
8 | MDT 100-18 Thruster Brake | ELECTRO HYDRAULIC THRUSTER BRAKE/MILL DUTY BRAKE 100x18 with 18 kg thruster,HSN Code:84312010 | MDT 100-18 | ![]() |
9 | MDT 150-18 Thruster Brake | ELECTRO HYDRAULIC THRUSTER BRAKE/MILL DUTY BRAKE 150x18 with 18 kg thruster ,HSN Code:84312010 | MDT 150-18 | ![]() |
10 | MDT 160-18 Thruster Brake | ELECTRO HYDRAULIC THRUSTER BRAKE/MILL DUTY BRAKE 160x18 with 18 kg thruster,HSN Code:84312010 | MDT 160-18 | ![]() |
11 | MDT 200-18 Thruster Brake | ELECTRO HYDRAULIC THRUSTER BRAKE/MILL DUTY BRAKE 200x18 with 18 kg thruster,HSN Code:84312010 | MDT 200-18 | ![]() |
12 | MDT 200-34 Thruster Brake | ELECTRO HYDRAULIC THRUSTER BRAKE/MILL DUTY BRAKE 200x34 with 34 kg thruster,HSN Code:84312010 | MDT 200-34 | ![]() |
13 | MDT 250-18 Thruster Brake | ELECTRO HYDRAULIC THRUSTER BRAKE/MILL DUTY BRAKE 250x18 with 18 kg thruster,HSN Code:84312010 | MDT 250-18 | ![]() |
14 | MDT 250-34 Thruster Brake | ELECTRO HYDRAULIC THRUSTER BRAKE/MILL DUTY BRAKE 250x34 with 34 kg thruster,HSN Code:84312010 | MDT 250-34 | ![]() |
15 | MDT 300-18 Thruster Brake | ELECTRO HYDRAULIC THRUSTER BRAKE/MILL DUTY BRAKE 100x18 with 18 kg thruster,HSN Code:84312010 | MDT 300-18 | ![]() |
16 | MDT 300-34 Thruster Brake | ELECTRO HYDRAULIC THRUSTER BRAKE/MILL DUTY BRAKE 300x34 with 34 kg thruster,HSN Code:84312010 | MDT 300-34 | ![]() |
17 | MDT 300-46 Thruster Brake | ELECTRO HYDRAULIC THRUSTER BRAKE/MILL DUTY BRAKE 300x46 with 46 kg thruster,HSN Code:84312010 | MDT 300-46 | ![]() |
18 | MDT 400-18 Thruster Brake | ELECTRO HYDRAULIC THRUSTER BRAKE/MILL DUTY BRAKE 400x18 with 18 kg thruster,HSN Code:84312010 | MDT 400-18 | ![]() |
19 | MDT 400-34 Thruster Brake | ELECTRO HYDRAULIC THRUSTER BRAKE/MILL DUTY BRAKE 400x34 with 34 kg thruster,HSN Code:84312010 | MDT 400-34 | ![]() |
20 | MDT 400-46 Thruster Brake | ELECTRO HYDRAULIC THRUSTER BRAKE/MILL DUTY BRAKE 400x46 with 46 kg thruster,HSN Code:84312010 | MDT 400-46 | ![]() |
21 | MDT 400-68 Thruster Brake | ELECTRO HYDRAULIC THRUSTER BRAKE/MILL DUTY BRAKE 400x68 with 68 kg thruster,HSN Code:84312010 | MDT 400-68 | ![]() |
22 | MDT 100-18 Only Brake | Thrusters Brake Assembly Without thruster , Drum Dia-100mm , HSN Code:84312010 | Brake-100-18 | ![]() |
23 | MDT 150-18 Only Brake | Brake-150-18kg only Brake with Brake Shoe without Thruster,HSN Code:84312010 | Brake-150-18 | ![]() |
24 | MDT 160-18 Only Brake | Brake-160-18kg only Brake with Brake Shoe without Thruster,HSN Code:84312010 | Brake-160-18 | ![]() |
25 | MDT 200-18 Only Brake | Brake-200-18kg only Brake with Brake Shoe without Thruster,HSN Code:84312010 | Brake-200-18 | ![]() |
26 | MDT 200-34 Only Brake | Brake-200-34kg only Brake with Brake Shoe without Thruster,HSN Code:84312010 | Brake-200-34 | ![]() |
27 | MDT 250-18 Only Brake | Brake-250-18kg only Brake with Brake Shoe without Thruster,HSN Code:84312010 | Brake-250-18 | ![]() |
28 | MDT 250-34 Only Brake | Brake-250-34kg only Brake with Brake Shoe without Thruster,HSN Code:84312010 | Brake-250-34 | ![]() |
29 | MDT 300-18 Only Brake | Brake-300-18kg only Brake with Brake Shoe without Thruster,HSN Code:84312010 | Brake-300-18 | ![]() |
30 | MDT 300-34 Only Brake | Brake-300-34kg only Brake with Brake Shoe without Thruster,HSN Code:84312010 | Brake-300-34 | ![]() |
31 | MDT 300-46 Only Brake | Brake-300-46kg only Brake with Brake Shoe without Thruster,HSN Code:84312010 | Brake-300-46 | ![]() |
32 | MDT 400-18 Only Brake | Brake-400-18kg only Brake with Brake Shoe without Thruster,HSN Code:84312010 | Brake-400-18 | ![]() |
33 | MDT 400-34 Ony Brake | Brake-400-34kg only Brake with Brake Shoe without Thruster,HSN Code:84312010 | Brake-400-34 | ![]() |
34 | MDT 400-46 Only Brake | Brake-400-46kg only Brake with Brake Shoe without Thruster,HSN Code:84312010 | Brake-400-46 | ![]() |
35 | MDT 400-68 Only Brake | Brake-400-68kg only Brake with Brake Shoe without Thruster,HSN Code:84312010 | Brake-400-68 | ![]() |
36 | BRAKE SHOE WITH LINER 100MM | BRAKE SHOE WITH LINER 100MM | BSL - 100MM | ![]() |
37 | BRAKE SHOE WITH LINER 150MM | BRAKE SHOE WITH LINER 150MM | BSL - 150MM | ![]() |
38 | BRAKE SHOE WITH LINER 160MM | BRAKE SHOE WITH LINER 160MM | BSL - 160MM | ![]() |
39 | BRAKE SHOE WITH LINER 200MM | BRAKE SHOE WITH LINER 200MM | BSL - 200MM | ![]() |
40 | BRAKE SHOE WITH LINER 250MM | BRAKE SHOE WITH LINER 250MM | BSL - 250MM | ![]() |
41 | BRAKE SHOE WITH LINER 300MM | BRAKE SHOE WITH LINER 300MM | BSL - 300MM | ![]() |
42 | BRAKE SHOE WITH LINER 400MM | BRAKE SHOE WITH LINER 400MM | BSL - 400MM | ![]() |
43 | BRAKE LINER 100MM DIA | BRAKE LINER 100MM DIA | BL-100MM | ![]() |
44 | BRAKE LINER 150MM DIA | BRAKE LINER 150MM DIA | BL-150MM | ![]() |
45 | BRAKE LINER 160MM DIA | BRAKE LINER 160MM DIA | BL-160MM | ![]() |
46 | BRAKE LINER 200MM DIA | BRAKE LINER 200MM DIA | BL-200MM | ![]() |
47 | BRAKE LINER 250MM DIA | BRAKE LINER 250MM DIA | BL-250MM | ![]() |
48 | BRAKE LINER 300MM DIA | BRAKE LINER 300MM DIA | BL-300MM | ![]() |
49 | BRAKE LINER 400MM DIA | BRAKE LINER 400MM DIA | BL-400MM | ![]() |
Understanding the Thruster Brake: Principles, Construction, and Operation
Thruster brakes are integral components in the world of machinery, playing a pivotal role in controlling the speed and halting the movement of equipment with precision. This article delves into the working principle, construction, and operation of thruster brakes, providing a comprehensive understanding of this crucial device.
Working Principle Of Hydraulic Thruster Brake
A thruster brake operates on a simple yet effective mechanism. When the brake is not energized, the brake shoes, under the influence of a pre-stressed compression spring, press against a brake drum attached to the drive motor shaft1. This application of braking force prevents the drum from rotating, effectively applying the brake1.
However, when the thruster motor is energized, it generates a thrust that lifts the crank lever1. This movement causes the arms to move, pulling the brake shoes away from the brake drum1. As a result, the braking force is released, allowing the drum to rotate1. The spring is compressed during this process, storing energy for the next braking cycle1.
Benefits of Thruster Brakes
1. Improved Safety: Thruster brakes enhance safety by providing reliable braking performance.
2. Increased Efficiency: Thruster brakes optimize crane operations, reducing cycle times.
3.
Reduced Maintenance: Thruster brakes require minimum maintenance.
Construction
A thruster brake is composed of several key components, each contributing to its efficient operation. The brake shoes, lined with friction pads, are hinged on the main arm and sidearm of the brake1. These arms are connected at the top by a tie rod, which is hinged in the main arm and locked to the swivel block in the sidearm1.
A crank lever, hinged on the main arm, is connected to the top clevis of the thruster1. A brake spring, fixed on the main arm, is pre-loaded by a lock nut on the lever1. The pre-tension in this spring determines the braking torque1. The thruster is fitted on the base by a hinge pin1.
Operation
The operation of a thruster brake is a seamless process. When the thruster is not energized, the brake shoes press on the brake drum, preventing it from rotating1. However, when the thruster motor is energized, the thrust lifts the crank lever, moving the arms and pulling the brake shoes away from the brake drum1. This action releases the braking force, allowing the drum to rotate1.
Conclusion
Thruster brakes are a testament to the marvels of engineering, combining simple principles with complex design to control the speed and movement of machinery. Understanding their working principle, construction, and operation can provide valuable insights into their role in various industrial applications.
Maximizing Efficiency with Electrohydraulic Thruster Brakes for EOT Cranes
Introduction
EOT (Electric Overhead Traveling) cranes have become indispensable in various industries, supporting the smooth movement of heavy loads across vast spaces. These cranes require reliable braking systems to ensure safe and efficient operations. Enter electrohydraulic thruster brakes for EOT cranes, a groundbreaking technology that combines the power of hydraulic systems with the precision of electrical controls.
With a focus on maximizing efficiency and safety, electrohydraulic thruster brakes have become the go-to choice for many industries. In this comprehensive article, we will delve into the various aspects of these brakes, including their thrust capacity, drum diameter options, usage in EOT cranes, brake sizes, fabrication techniques, and more.
Advancements in Braking Technology
Understanding Electrohydraulic Thruster Brakes
Electrohydraulic thruster brakes provide robust braking capabilities by combining the fluid power of hydraulics with the superior control of electrical systems. These brakes are designed to offer precise braking action with quick response times, which is crucial in maximizing operational safety.
The brake system comprises a thruster, brake shoe assembly, hydraulic cylinder, and applying springs, all working in tandem to deliver the required braking force. When engaged, the thruster applies hydraulic pressure to the brake shoe assembly, causing friction against the braking surface and bringing the crane to a stop.
Key Features of Electrohydraulic Thruster Brakes
Various Thrust Capacities
Electrohydraulic thruster brakes are available in a wide range of thrust capacities, making them suitable for various types of EOT cranes. Whether you are operating a mini EOT crane or a heavy-duty industrial crane, there is a brake specifically designed to match your requirements. The thruster capacity determines the maximum braking force the brake can generate, ensuring safety during crane operation.
Drum Diameter Options
Different EOT cranes have varying drum diameters, and selecting the appropriate brake ensures optimal performance. Electrohydraulic thruster brakes come in an array of sizes to accommodate different drum diameters accurately. This compatibility guarantees efficient braking action and prevents slippage, increasing the overall reliability of the system.
Enhancing Safety with Precision
Safety is paramount in any crane operation, and electrohydraulic thruster brakes excel in this area. These brakes provide precise control over the braking action, ensuring smooth and accurate stops without any overrun. This precision not only enhances worker safety but also prevents potential damage to goods and equipment being lifted, lowering the risk of accidents and costly downtime.
Fabrication Techniques
Electrohydraulic thruster brakes for EOT cranes are fabricated using high-quality materials that undergo rigorous testing to meet industry standards. State-of-the-art manufacturing processes and stringent quality control measures play a crucial role in ensuring the reliability and durability of these brakes. With their robust construction, electrohydraulic thruster brakes can withstand the harsh operating conditions typically experienced in heavy-duty industries.
FAQs (Frequently Asked Questions)
1. What is the working principle of electrohydraulic thruster brakes for EOT cranes?
The thruster applies hydraulic pressure to the brake shoe assembly, generating friction against the braking surface, resulting in the desired braking force.
2. What factors should be considered when selecting an electrohydraulic thruster brake?
Crucial factors to consider include thrust capacity, drum diameter compatibility, and the specific requirements of the EOT crane.
3. How does precision braking enhance safety during crane operations?
Precision braking prevents overrun and ensures accurate stops, minimizing the risk of accidents and damage to goods and equipment.
Conclusion
Electrohydraulic thruster brakes for EOT cranes have revolutionized braking technology, introducing precise control and enhanced safety to crane operations. With their various thrust capacities and drum diameter options, these brakes can be tailored to suit the needs of any EOT crane, offering optimal performance and increased efficiency.
Their robust fabrication techniques and impeccable reliability make them an ideal choice for heavy-duty industries. By maximizing safety, accuracy, and control, electrohydraulic thruster brakes pave the way for seamless crane operations, ensuring the smooth movement of loads and promoting productivity across various sectors.